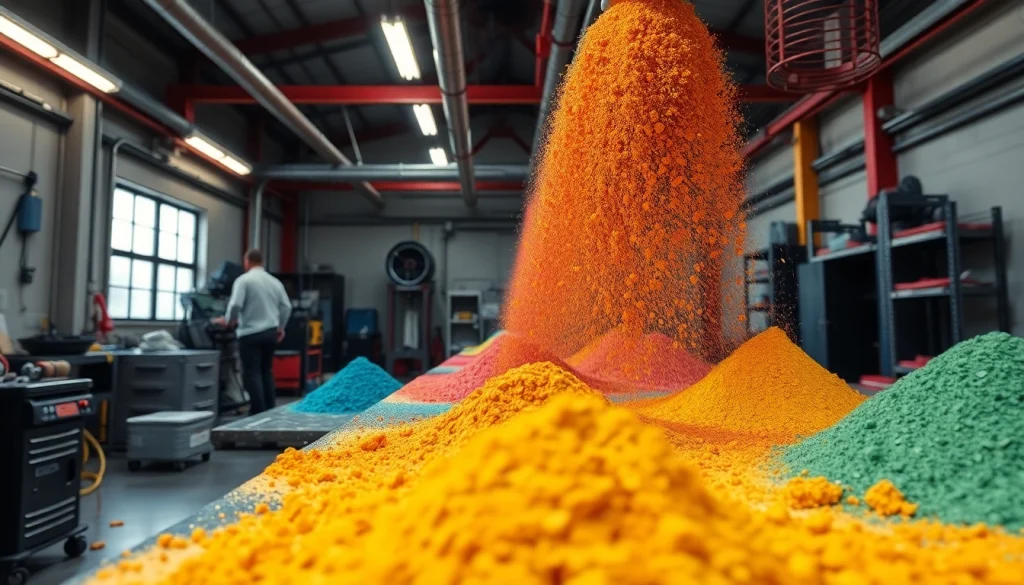
Understanding Powder Coating
What is Powder Coating and How Does It Work?
Powder coating is a dry finishing process that involves applying a fine powder to a surface, typically metals, which is then heated to create a durable and protective layer. Unlike conventional liquid paints, powder coatings do not require solvents and are applied as a free-flowing, dry powder. The coating is electrostatically charged, which helps it adhere to the surface more effectively before being cured in an oven. Once heated, the powder melts and fuses into a smooth, even coating that is both aesthetically pleasing and extremely durable.
This process is not only efficient but also environmentally friendly, reducing volatile organic compounds (VOCs) that are typically released during liquid paint application. The versatility of powder coating allows it to be used in various industries, from automotive to architectural applications.
The Chemistry Behind Powder Coatings
Powder coatings are primarily composed of polymer resin systems that are combined with a variety of additives, including curatives, pigments, leveling agents, and flow modifiers. The common types of resins used include:
- Epoxy Resins: Known for their excellent adhesion and corrosion resistance, making them ideal for heavy-duty applications.
- Polyester Resins: Offer good weather resistance and color stability, suitable for outdoor applications.
- Acrylic Resins: Known for their gloss and excellent UV resistance, giving vibrant finishes.
These resins undergo a chemical reaction during the curing process, typically at temperatures between 350°F (177°C) and 400°F (204°C), which enhances their mechanical and chemical properties.
Common Applications of Powder Coating
Powder coating is widely used in various sectors, demonstrating its versatility. Some of the most common applications include:
- Automotive Industry: Used for coating parts like wheels, chassis, and trim to provide durable finishes.
- Architectural Applications: Employed for exterior building components such as window frames and railings, offering both protective and aesthetic qualities.
- Furniture and Home Appliances: Furniture items gain durability and color through powder coating, while home appliances enjoy a robust finish that resists scratches and corrosion.
- Industrial Equipment: Heavy machinery parts are often powder coated to prevent rust and wear in harsh environments.
Benefits of Powder Coating
Durability and Resistance Features
One of the most compelling reasons to choose powder coating is its superior durability. The baked finish is more resistant to chips, scratches, corrosion, and fading compared to traditional paint. Additionally, powder coating is less prone to showing fingerprints and smudges, maintaining its clean appearance. Its ability to withstand extreme environmental conditions, including high temperatures and harsh chemicals, makes it an ideal choice for industrial applications.
Environmental Benefits of Powder Coating
Powder coating is also recognized for its ecological advantages. Because it uses a dry application process, it generates minimal waste. Any overspray can be collected and reused, at times making the overall process highly efficient regarding materials used. Furthermore, the absence of solvents in powder coatings means that VOC emissions are significantly lower than those associated with liquid paints. This makes it a more sustainable choice for businesses looking to reduce their environmental impact.
Cost-Effectiveness Compared to Other Finishes
When evaluating the cost, powder coating often provides better value than liquid paints over its lifecycle. Initially, the application may require a higher investment in equipment and setup. However, the durability and longevity of the powder finish translate into lower maintenance and repair costs down the line. Moreover, its resistance to wear means that items coated with powder typically have a longer lifespan, reducing the need for frequent refinishing.
Choosing the Right Powder Coating
Factors to Consider Before Selecting Powder Coats
When selecting a powder coating for your project, several factors come into play:
- Application Method: Determine what application method you’ll use—electrostatic spraying, fluidized bed, or other techniques will influence your powder choice.
- Environment: Consider the environment the coated item will face. For outdoor applications, select coatings designed for UV resistance.
- Finish Type: Decide on the finish desired (matte, glossy, textured, or satin) to ensure the right powder selection.
- Durability Requirements: Evaluate the need for impact resistance, adhesion, and overall performance based on use.
Popular Powder Coating Color Options
The palette of colors available in powder coatings is vast. Popular options include:
- Metallic Finishes: These provide a shiny appearance and are often used for custom automotive parts.
- Textured Coatings: Ideal for hiding surface imperfections and providing additional grip.
- Matte and Satin Finishes: Offer a sophisticated look that aligns with modern design aesthetics.
- RAL Colors: Compliance with standard color charts allows consistent and recognizable finishes across products.
Matching Your Finish with Project Needs
It is crucial to match the finish of the powder coating with the specific needs of a project. For example, heavy machinery may require a thicker, more robust finish, while consumer products like electronics might benefit from a thinner coat that achieves a sleek look. Understanding the performance expectations helps in achieving both functional and visual goals.
Powder Coating Techniques and Tools
Essential Equipment for Powder Coating
Having the right equipment is vital for effective powder coating application. Essential tools include:
- Powder Coating Gun: A high-voltage electrostatic gun is used to apply the powder evenly.
- Curing Oven: Necessary for melting and curing the powder to create a durable finish.
- Wash Station: Prepping surfaces through cleaning is critical, and a wash station aids in this process.
- Hanging Racks: To ensure that pieces are hung securely and avoid powder contamination.
DIY vs Professional Powder Coating Services
Deciding between a DIY approach and hiring a professional service often depends on the complexity of the project and available resources. DIY powder coating can be cost-effective for small, simple parts, especially with equipment becoming more affordable. However, professional services come with expertise and established processes that can ensure high-quality results for larger or more intricate items, making it worthwhile to invest in professional services for significant projects.
Best Practices for High-Quality Finishes
To achieve the best possible powder-coated finish, follow these best practices:
- Surface Preparation: Ensure thorough cleaning and prep of surfaces to promote adhesion.
- Consistent Application: Use steady and even strokes when applying powder to avoid uneven coverage.
- Cure Properly: Always follow the manufacturer’s guidelines for curing times and temperatures to achieve optimal thickness and durability.
- Inspect Finished Products: Perform a final inspection for any imperfections or inconsistencies post-cure.
Maintenance and Care for Powder Coated Surfaces
How to Clean and Maintain Powder Coatings
Maintaining powder coated surfaces is relatively straightforward. Regular cleaning with mild soap and water helps prevent the buildup of dirt and contaminants. Avoid harsh chemicals that might damage the finish. For tougher stains, a soft-bristled brush can facilitate removal without scratching the surface.
Addressing Common Issues with Powder Coated Items
While powder coatings are highly durable, some common issues may arise:
- Chipping: Caused by impact; can often be repaired by spot-recoating the affected area.
- Fading: Can occur from prolonged exposure to UV light; selecting UV-resistant powders at the outset helps curb this.
The Longevity of Powder Coated Products
Powder coating significantly extends the lifespan of products. Properly coated items can resist corrosion for many years, making them a popular choice for items subjected to harsh conditions. Routine maintenance contributes to this longevity, ensuring that products retain their beautiful appearance and protective qualities throughout their lifespan.