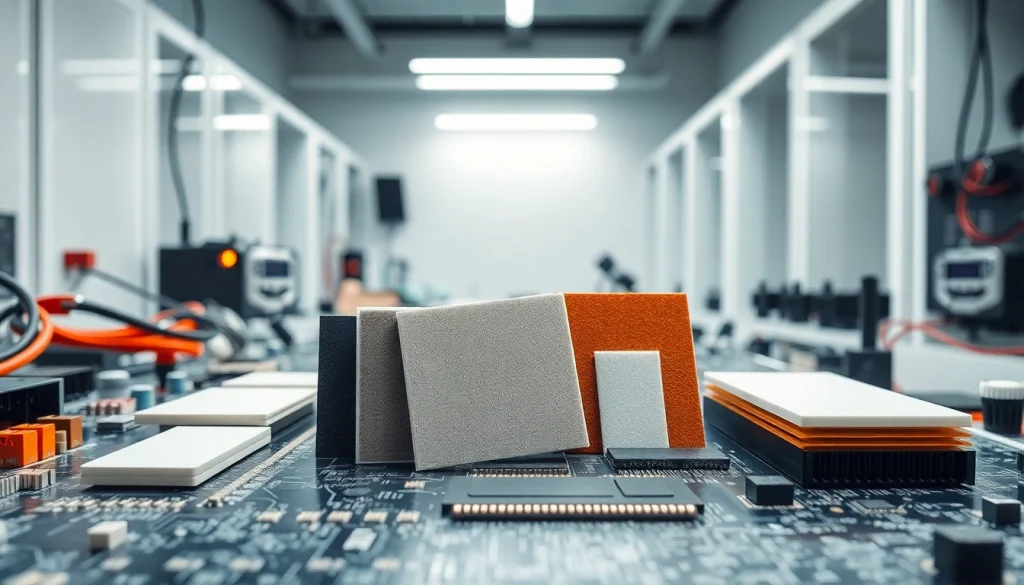
Understanding Thermal Management Materials
In an era where electronic devices are becoming smaller and more powerful, effective heat dissipation has become a crucial aspect of design and manufacturing. Thermal management materials play a significant role in managing heat generated by electronic components, ensuring their reliability, performance, and longevity. By efficiently channeling and dissipating heat, these materials help maintain operational temperatures within safe limits, thereby enhancing the overall performance of electronic systems.
What are Thermal Management Materials?
Thermal management materials are specially engineered substances designed to facilitate the transfer and dissipation of heat in various applications, particularly in electronics. These materials encompass a broad range of types, including gap fillers, thermal interface materials (TIMs), adhesives, and phase change materials, each tailored for specific thermal management needs.
Essentially, thermal management materials can be categorized based on their function, thermal conductivity, and application requirements. They serve to minimize thermal resistance between heat-generating components and their heat sinks or surrounding environment, thereby improving cooling efficiency.
Types of Thermal Management Materials
The diverse spectrum of thermal management materials includes:
- Thermal Interface Materials (TIMs): These materials facilitate heat transfer between surfaces and can range from thermal greases to pads and tapes.
- Gap Filler Materials: Used to fill the voids between components and heatsinks, enhancing contact area and thermal conductivity.
- Thermal Adhesives: These are used for bonding components while also providing necessary thermal conductivity.
- Phase Change Materials (PCMs): Materials that absorb, store and release thermal energy during phase transitions, effectively smoothing out temperature fluctuations.
- Thermal Gels and Pastes: These substances improve thermal contact and lessen thermal resistance in critical applications.
Applications and Importance in Electronics
Thermal management materials find applications across various sectors, especially in electronics where managing heat is vital for performance and safety. Key applications include:
- Consumer Electronics: In devices like smartphones and laptops, effective thermal management is necessary to prevent overheating and ensure the reliability of components over extended use.
- Automotive: In electric vehicles (EVs), thermal management materials help control battery temperatures and optimize performance efficiency.
- Telecommunications: Equipment such as servers and base stations require efficient cooling to maintain operational integrity.
- Aerospace: High-performance systems require stringent thermal management to ensure safety and functionality at extreme operating conditions.
Key Properties of Thermal Management Materials
Thermal Conductivity and Resistance
The most critical property of any thermal management material is its thermal conductivity, which quantifies a material’s ability to conduct heat. High thermal conductivity (measured in watts per meter-Kelvin, W/mK) is vital for effective heat transfer, thereby lowering thermal resistance between interfaces.
Different materials exhibit varying thermal conductivities, making the selection of the right material crucial for the effectiveness of thermal management systems. For example, metals like copper and aluminum offer high conductivity, while polymer-based materials provide lower but often adequate conductivity for specific applications.
Durability and Stability
Durability refers to a material’s ability to withstand mechanical stress and thermal cycling over its lifespan. Stability, on the other hand, involves maintaining performance characteristics under varying environmental conditions. For electronic applications, materials must cope with thermal expansion and contraction, humidity, and potential chemical exposure.
Materials like silicone-based thermal compounds are known for their excellent durability and stability, making them suitable for long-term applications in electronics.
Environmental Impact and Compliance
As sustainability becomes increasingly significant, selecting thermal management materials that comply with environmental regulations is essential. Manufacturers should consider materials that minimize environmental impact, such as those free from hazardous substances and those that can be recycled or are biodegradable.
Compliance with regulations like RoHS (Restriction of Hazardous Substances) and REACH (Registration, Evaluation, Authorisation, and Restriction of Chemicals) is crucial for businesses looking to market their products globally.
Choosing the Right Thermal Management Material
Factors to Consider for Selection
The selection of thermal management materials is influenced by various factors, including:
- Thermal performance requirements: Consider the necessary thermal conductivity based on the application.
- Mechanical properties: Assess the need for flexibility or rigidity, depending on mounting configurations.
- Environmental conditions: Understand the operating conditions such as temperature ranges and exposure to chemicals or moisture.
- Application-specific requirements: Assess needs such as adhesion, conformability, and ease of application.
Common Use Cases Across Industries
Thermal management materials can be observed across numerous sectors:
- Electronics: Mobile devices employ thermal interface materials to ensure efficient heat dissipation.
- Industrial Equipment: Heavy machinery utilizes thermal gels for effective component cooling.
- Aerospace: Thermal adhesives provide bond strength while managing temperatures in aircraft components.
Cost vs. Performance Analysis
A comprehensive cost-benefit analysis is vital in selecting thermal management materials. Higher performance materials may carry a higher upfront cost but can result in long-term savings through improved efficiency and reduced maintenance costs. It is essential to weigh these factors against the operational importance of thermal management within the specific application context.
Best Practices for Implementing Thermal Management Materials
Installation Techniques for Optimal Performance
Ensuring optimal performance of thermal management materials begins with proper installation. Best practices include:
- Surface Preparation: Clean surfaces to eliminate contaminants that could impair adhesion and thermal conductivity.
- Application Method: Employ recommended application techniques such as precise thickness and uniform distribution of materials.
- Clamping Pressure: Apply appropriate pressure to increase contact area while preventing damage to components.
Innovative Solutions in Thermal Management
With ongoing advancements in material science and engineering, new solutions for thermal management are emerging. Nanotechnology, for example, has led to the development of advanced thermal interface materials with improved conductivity. Similarly, innovative liquid cooling technologies are becoming mainstream, offering efficient ways to manage heat in high-performance applications.
Case Studies and Success Stories
Real-world applications illustrate the effectiveness of thermal management materials. For instance, a leading semiconductor manufacturer implemented custom thermal interface materials in their chip packaging, resulting in a 20% improvement in heat dissipation compared to conventional materials. These advancements enabled higher performance and reliability of their products in competitive markets.
Future Trends in Thermal Management Materials
Emerging Technologies and Innovations
As technology continues to evolve, the future of thermal management materials is bright. Emerging materials such as graphene and metal matrix composites offer the promise of new solutions with exceptional thermal properties. Innovations in smart materials with self-regulating thermal management capabilities are also being researched, paving the way for more efficient and adaptable thermal solutions.
Market Trends and Expected Developments
The market for thermal management materials is poised for growth driven by increasing demand for high-performance electronics, electric vehicles, and renewable energy technologies. As regulatory frameworks around environmental compliance strengthen, the need for sustainable materials will amplify, influencing market dynamics.
Expert Insights on Next Steps
For businesses looking to stay competitive, it is crucial to keep abreast of developments in thermal management materials. Collaboration with material suppliers can yield insights into the latest technologies and their applicability, while investing in research and development can lead to innovative solutions tailored for specific applications.