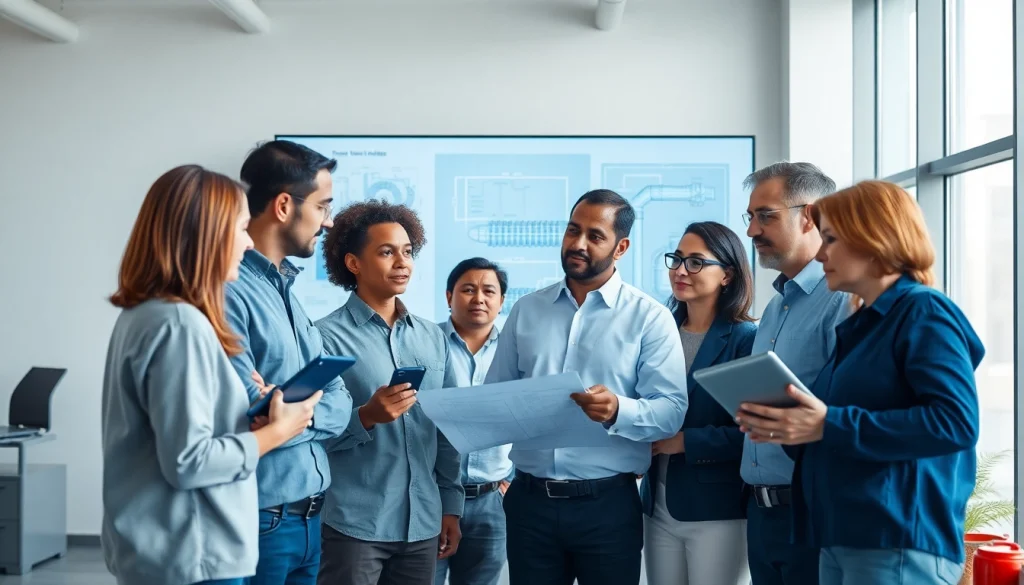
Understanding Piping Stress Analysis
What is Piping Stress Analysis?
Piping stress analysis is a crucial engineering discipline that focuses on the evaluation of stresses in piping systems under various conditions. The primary objective is to ensure the integrity of piping during operation and its ability to withstand external and internal forces which may include temperature fluctuations, pressure changes, and gravitational loads. By assessing these stresses, engineers can predict potential failures or leaks in the piping systems, avoiding catastrophic failures and significant monetary losses.
Importance of Piping Stress Analysis in Engineering
In various industries such as oil and gas, chemical processing, and power generation, the reliability of piping systems is of utmost importance. A comprehensive understanding of piping systems is essential for any piping stress Analysis Company. Piping stress analysis plays a vital role in ensuring safety, environmental protection, and compliance with industry regulations. It aids engineers in designing robust systems that prevent hazardous leaks or structural failures. Moreover, rigorous stress analysis can extend the lifespan of piping systems and optimize maintenance schedules, ultimately reducing operational downtime and maintenance costs.
Common Methods Used in Piping Stress Analysis
Piping stress analysis can be performed using a variety of methods, each with its own advantages and suitability depending on the project requirements. Some of the common methods include:
- Static Analysis: This approach evaluates the effects of static loads such as weight, pressure, and temperature on the piping system.
- Dynamic Analysis: This method assesses how piping systems respond to dynamic loads, such as seismic events or pressure fluctuations.
- Finite Element Analysis (FEA): FEA involves using computer-based models to simulate the behavior of piping systems under various loads and conditions, providing detailed insights into stress distribution.
- Allowable Stress Design (ASD): A method that uses predefined allowable stress limits for materials to ensure safety factors are integrated into the design.
Key Considerations for Piping Stress Analysis
Factors Affecting Piping Stress
A wide range of factors contributes to the stresses encountered in piping systems. Understanding these factors is essential for effective stress analysis. Key considerations include:
- Temperature Variations: Changes in temperature can lead to expansion or contraction in the piping, which induces thermal stress.
- Internal and External Pressures: High-pressure conditions can exert significant stress on pipes, leading to deformation or failure if not properly managed.
- Support and Restraint Conditions: The way a pipe is supported can greatly affect its ability to handle stress. Proper support design is essential to prevent excessive bending or forces.
- Material Properties: Different materials respond differently to stress, temperature changes, and corrosion, making it essential to select the right material for the specific application.
Standard Codes and Regulations
Industry standards and codes provide guidelines for performing piping stress analysis and ensuring compliance with safety and operational requirements. Recognized standards include:
- ASME B31 Series: The American Society of Mechanical Engineers has developed piping codes that specify design, materials, fabrication, and testing requirements.
- API 570: This code focuses on in-service inspection, rating, repair, and alteration of piping systems in the petroleum and chemical industries.
- ISO 14692: This international standard covers the design, installation, and maintenance of glass-reinforced plastic piping systems.
Best Practices in Performing Stress Analysis
To achieve the best results in piping stress analysis, engineers should adhere to several best practices:
- Comprehensive Data Collection: Gather all relevant data, including material properties, operational conditions, and historical performance records.
- Utilize Advanced Software: Employ state-of-the-art analysis software that facilitates accurate modeling and simulation for better predictive capabilities.
- Conduct Regular Reviews: Frequent reviews of piping systems and stress analyses can help identify improvements and preemptively solve potential issues.
- Train Engineers Continuously: Ensure team members are up-to-date on the latest practices, software tools, and industry standards through ongoing training.
Tools and Software for Piping Stress Analysis
Popular Software Solutions for Engineers
The adoption of specialized piping stress analysis software can significantly enhance the accuracy and efficiency of assessments. Some popular software solutions include:
- CAESAR II: Widely recognized for its robust capabilities in analyzing complex piping systems, it offers extensive features for static and dynamic analysis.
- ANSYS: This comprehensive simulation tool enables engineers to conduct advanced stress analysis along with other mechanical simulations.
- AutoPIPE: A user-friendly tool designed for easy use in design and analysis of piping systems, emphasizing code compliance.
- SolidWorks: While primarily a CAD tool, it can integrate with other software to handle stress analysis for designed systems.
Choosing the Right Software for Your Needs
Selecting the appropriate software for piping stress analysis depends on specific project requirements, including complexity, budget, and integration needs. Consider the following factors:
- Project Size and Complexity: Choose software that can effectively handle the scale of your projects, whether small or large-scale operations.
- Compatibility with Other Tools: Ensure the software can seamlessly integrate with other engineering tools for a unified workflow.
- Support and Training: Opt for solutions with strong customer support and training resources to help your team maximize the software’s potential.
Integrating Software Tools into Your Workflow
To fully leverage the benefits of piping stress analysis software, integration into established workflows is essential. This can be achieved by:
- Defining Clear Protocols: Establish clear processes for using software tools within the stress analysis protocol to ensure consistency.
- Encouraging Team Collaboration: Utilize collaborative features of software to allow multiple team members to contribute to the analysis process effectively.
- Regular Upgrades and Updates: Keep software updated to benefit from the latest features and improvements in the analysis capabilities.
Case Studies on Piping Stress Analysis
Successful Projects from Leading Companies
Real-world applications of piping stress analysis highlight the effectiveness of strategic engineering practices. For instance, a prominent oil and gas company employed advanced stress analysis techniques during a plant expansion to ensure new piping systems integrated seamlessly with existing infrastructure. By using finite element analysis, the company successfully mitigated potential stress issues, leading to on-time project completion and significant cost savings.
Lessons Learned from Failures
While many projects have benefited from effective stress analysis, there are notable cases where neglecting proper assessments led to disasters. A chemical plant experienced a catastrophic failure due to improper stress analysis on its piping. The incident caused injuries and substantial financial loss, underscoring the necessity of rigorous analysis and adherence to codes and standards as mandated in the industry.
Application of Stress Analysis in Real-world Scenarios
Piping stress analysis is not limited to design and installation phases; it also plays a significant role in ongoing maintenance and inspections. For instance, the refurbishment of an aging pipeline system in a power plant incorporated advanced stress analysis to evaluate the integrity of materials and structures, facilitating informed decisions about repairs and maintaining operational safety.
Future Trends in Piping Stress Analysis
Emerging Technologies in Engineering
The field of piping stress analysis is evolving as new technologies emerge. Innovations like 3D printing for custom piping solutions and advanced materials that offer better resilience to stress are likely to revolutionize how engineers approach design and analysis. Such advancements can lead to enhanced operational efficiency and extended system lifespans.
The Role of AI in Piping Stress Analysis
Artificial intelligence is making significant inroads into engineering disciplines, including piping stress analysis. AI-driven software can analyze vast amounts of data to identify patterns and predict stress points more accurately. By incorporating machine learning algorithms, engineers can enhance predictive maintenance, leading to improved safety and cost efficiency.
Preparing for Changes in Industry Standards
As technology evolves, industry standards for piping stress analysis will also adapt. Companies must remain vigilant and proactive in staying updated on emerging regulations. This will involve continued education for engineers, investment in advanced analytic tools, and fostering a culture of safety and compliance within engineering teams. By anticipating changes, companies can build more robust systems that thrive amidst evolving industry landscapes.