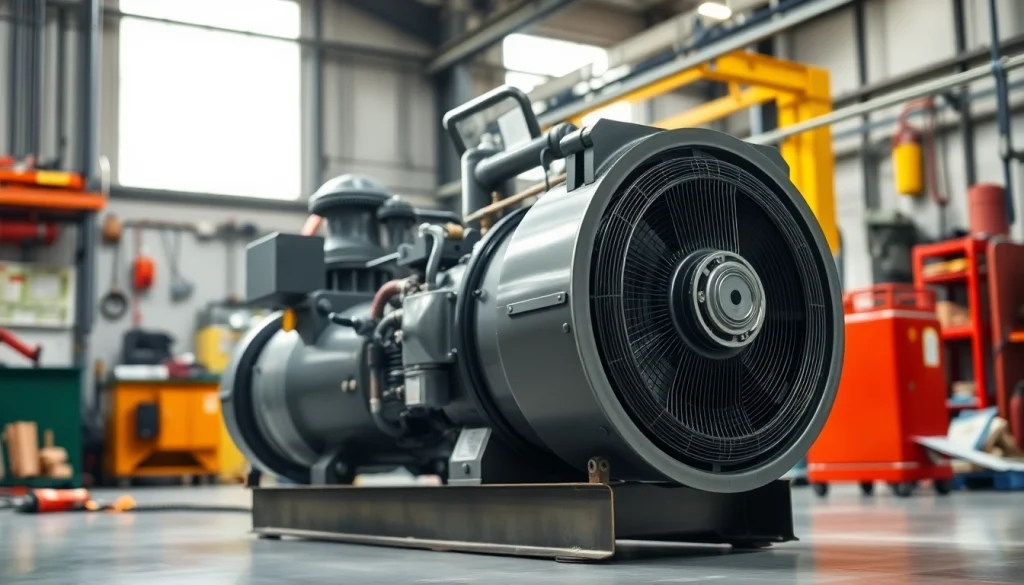
Understanding Industrial Air Compressors
Industrial air compressors are vital components in various manufacturing and production processes. These machines convert power into potential energy stored in compressed air, which can be utilized for multiple applications. They serve as the backbone for numerous industries, powering tools, equipment, and processes. As industries evolve, the demand for efficient and reliable air compressors has spurred innovations among industrial air compressor manufacturers, creating a competitive market landscape.
What is an Industrial Air Compressor?
An industrial air compressor is a device designed to compress air for industrial applications. It uses mechanical energy—often generated by an electric motor or diesel engine—to compress the air, thus increasing its pressure. The function of the air compressor is not merely to store air; rather, it plays a critical role in a majority of industrial operations, from pneumatic tools to air-driven machinery, and even for transporting materials in certain manufacturing scenarios.
Types of Industrial Air Compressors
Understanding the types of air compressors is essential when selecting one for specific applications. The major categories include:
- Reciprocating Compressors: Often termed piston compressors, these are typically used for lower volume requirements and produce high pressures. They are ideal for applications needing rapid bursts of air.
- Rotary Screw Compressors: Common in industrial applications, these compressors provide continuous air flow and are highly efficient, making them suitable for larger operations.
- Scroll Compressors: These are notable for their quiet operation and efficiency. They’re often used in smaller operations requiring a steady source of compressed air.
- Centrifugal Compressors: Suited for high-volume and low-pressure applications, these utilize a rotating disk to compress air and are often found in large industrial settings.
Applications and Industries Utilizing Compressors
Industrial air compressors have diverse applications across multiple sectors:
- Manufacturing: Air compressors are commonly used for powering pneumatic tools, material handling systems, and assembly lines.
- Construction: They are indispensable in construction sites for powering nail guns, jackhammers, and air chisels.
- Food and Beverage: Compressed air is used in food packaging, processing, and bottling operations.
- Automotive: In the automotive industry, compressors are crucial for spray painting and powering pneumatic tools.
- Pharmaceuticals: Compressed air must meet strict contamination standards and is used in processes requiring sterile environments.
Top Industrial Air Compressor Manufacturers
Leading Brands in the Market
The industrial air compressor market is dominated by several reputable brands known for their quality and innovation. Leading manufacturers include:
- Ingersoll Rand: This brand is well-known for its diverse range of high-quality compressors, ensuring efficiency and reliability across various applications.
- Atlas Copco: Known for its innovative technologies, Atlas Copco provides energy-efficient solutions that cater to the modern industry.
- Eaton Compressor: They focus on manufacturing robust compressors designed to withstand heavy usage, explicitly aimed at commercial and industrial applications.
- ELGi Compressors: Offers a variety of portable and stationary air compressors that are eco-friendly and designed to reduce energy costs.
- Kaeser Compressors: This company emphasizes quality and endurance in its rotary screw compressors, suitable for industrial applications with high demands.
Manufacturer Comparison and Features
When choosing an industrial air compressor, comparing the features of each manufacturer can help determine the best fit for specific needs. Key factors to consider include:
- Energy Efficiency: Brands such as Atlas Copco and ELGi focus on designing compressors that reduce overall energy consumption.
- Durability: Eaton and Kaeser compressors are engineered for tough conditions, providing robust performance over long periods.
- Noise Levels: Scroll and rotary screw compressors typically produce less noise, making them more suitable for environments where noise minimization is essential.
Customer Feedback and Reliability Ratings
Customer testimonials and reliability ratings play a vital role in selecting the right air compressor manufacturer. Feedback can often highlight the following:
- Quality of Service: Positive customer experiences often emphasize strong service and support from manufacturers, which is critical in maintaining industrial operations.
- Performance Under Load: Many users report reliability, especially in high-demand environments, which can influence long-term efficiency and cost-effectiveness.
- Repair and Maintenance: Customer feedback often notes the availability of replacement parts and ease of service, affecting overall customer satisfaction.
Factors to Consider When Choosing a Manufacturer
Quality and Performance Standards
When selecting an industrial air compressor, it is crucial to evaluate the quality and performance standards upheld by the manufacturer. Look for certifications such as ISO 9001, which ensure adherence to international quality management systems. Reviewing performance metrics such as CFM (Cubic Feet per Minute), PSI (Pounds per Square Inch), and the duty cycle of the compressor can provide insight into its operational efficiency.
Service and Support Options
Reliable customer service and support options are essential. Inquire about the following:
- Warranty Terms: Solid warranties can protect against early failures and provide peace of mind.
- Technical Support: Access to technical assistance and troubleshooting resources can significantly reduce downtime during operational issues.
- Training Programs: Some manufacturers offer training for staff on how to operate and maintain equipment, which can enhance productivity and safety.
Cost vs. Value Analysis
While price is often a key consideration, evaluating the value for money is equally important. Consider total cost of ownership, which includes:
- Initial purchase price
- Operating and maintenance costs
- Potential downtime
- Energy efficiency and savings over time
This comprehensive perspective ensures that the compressor you select is not just affordable but also cost-effective in the long run.
Best Practices for Sourcing Industrial Air Compressors
Researching Manufacturer Reputation
Before finalizing a purchase, thorough research on the manufacturer’s reputation is vital. Reputable sources can include:
- Industry reviews and ratings
- Professional recommendations and networks
- Customer testimonials and case studies from current users
Platforms such as trade shows and industry expos can also provide valuable firsthand insights.
Importance of After-Sales Service
After-sales service is critical to maintaining an industrial air compressor’s performance. Ensure that the manufacturer provides:
- Routine maintenance services
- Rapid response times for repairs
- Access to genuine spare parts and inventory
Strong after-sales support can prevent minor issues from escalating into costly downtime.
Understanding Warranty and Maintenance Services
A comprehensive understanding of warranty policies is essential. Review what is covered under warranty and for how long, as well as maintenance services included with purchase. Regular preventive maintenance can extend the lifespan of the compressor, ensuring it operates at peak efficiency.
Future Trends in Industrial Air Compressor Manufacturing
Technological Advances in Air Compressors
The air compressor industry is on the brink of significant technological advancements. Innovations such as IoT (Internet of Things) integration allow for real-time monitoring and diagnostics. This can help manufacturers analyze compressor performance, predict maintenance, and optimize operating conditions for improved efficiency.
Environmental Considerations and Innovations
Sustainability is becoming increasingly critical in manufacturing. Many industrial air compressor manufacturers are investing in technologies that reduce carbon emissions and energy consumption. Examples include:
- Use of variable speed drives that adjust speed based on demand
- Development of oil-free compressors that minimize environmental impact
- Implementation of energy recovery systems that capture waste heat for reuse
Market Projections for Air Compressor Demand
Market analysts predict a steady growth trajectory for the industrial air compressor sector, driven by expanding manufacturing activities, renewable energy trends, and industrial automation. The demand for energy-efficient and environmentally friendly solutions is expected to further fuel growth in this segment, offering promising opportunities for both manufacturers and customers.