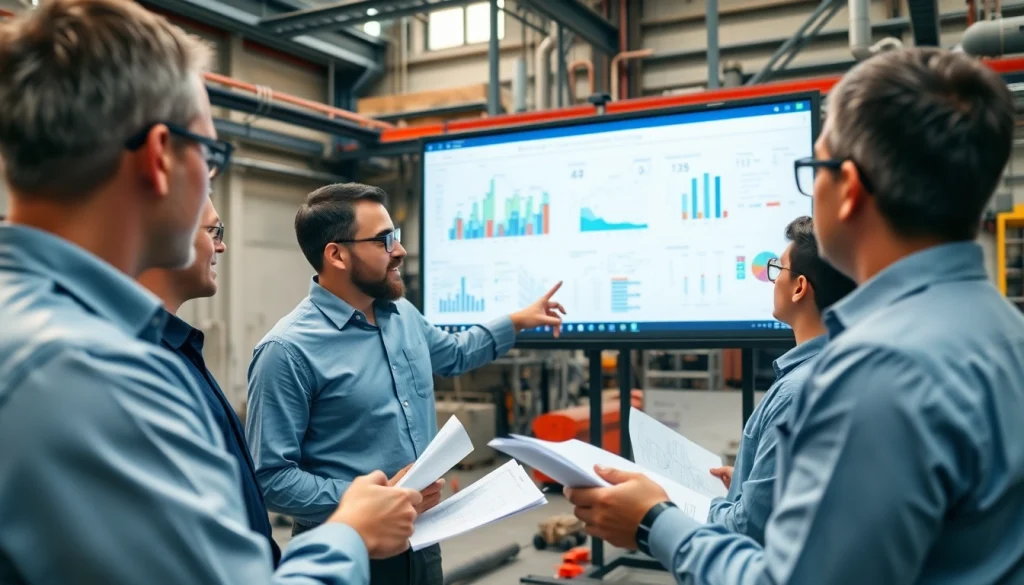
Piping Stress Analysis: An Overview
Piping stress analysis is a critical engineering discipline that ensures the functional reliability and safety of piping systems used in various industries, such as oil and gas, chemical manufacturing, power generation, and pharmaceuticals. By understanding the stresses that develop in pipes during operation, engineers can design systems that effectively mitigate these stresses, thereby preventing failures that could lead to costly downtimes or hazardous situations. A credible piping stress Analysis Company employs detailed methodologies to assess and optimize piping systems, balancing flexibility, support, and load conditions.
What is Piping Stress Analysis?
Piping stress analysis involves evaluating the mechanical integrity of pipe systems to ensure they can withstand operational stresses over their intended lifespan. This process includes the calculation of thermal expansion, weight, pressure, and dynamic loads, all of which contribute to the overall stress on piping. In cases where the calculated stresses exceed acceptable limits, corrective measures such as design modification and additional supports may be necessary to ensure compliance with industrial standards and regulations.
Importance of Piping Stress Analysis in Engineering
The importance of piping stress analysis cannot be overstated. It serves several key purposes:
- Safety Assurance: Identifying potential stress failures minimizes the risk of catastrophic incidents, safeguarding both personnel and the environment.
- Cost-Efficiency: By preventing leaks and failures, companies can save significantly on repair costs and environmental cleanup.
- Compliance: Adhering to industry codes and regulations helps organizations avoid legal repercussions and maintain their reputation.
Key Components of a Piping Stress Analysis
A comprehensive piping stress analysis encompasses several components:
- Load Cases: Analyzing different operational scenarios, including static and dynamic loads, helps anticipate various stress conditions.
- Material Properties: Understanding the physical and thermal properties of materials used in the piping system is crucial for accurate stress evaluations.
- Boundary Conditions: These conditions are crucial in defining how the piping system interacts with its environment.
- Support Systems: The design and placement of supports directly influence the stress distribution along the piping.
Understanding the Methods Used by Piping Stress Analysis Companies
Numerical Analysis Techniques
Piping stress analysts frequently employ numerical analysis techniques to model complex systems and predict how they will react under various conditions. These techniques may include linear and nonlinear analyses, which help engineers visualize potential stress points across the system. The effectiveness of these techniques lies in their ability to handle intricate geometries and loading scenarios that traditional analytical methods may not manage effectively.
Finite Element Analysis (FEA) Explained
Finite Element Analysis (FEA) is a cornerstone of modern piping stress analysis. This numerical method divides complex structures into smaller, manageable elements, allowing for detailed examination of stress distribution and deformation under various load conditions. Engineers input material properties, boundary conditions, and loading scenarios into FEA software, yielding a comprehensive stress analysis that informs design modifications. The robustness of FEA makes it a preferred method for intricate piping systems, ensuring they operate safely and efficiently.
Comparative Case Studies of Piping Systems
Studying existing piping systems helps identify best practices and common pitfalls in piping stress analysis. For example, a case study of a high-pressure gas pipeline reveals how inadequate support led to fatigue failure, prompting engineering teams to re-evaluate support placement practices. In another instance, a power plant’s cooling water system showcased the effective use of expansion joints to accommodate thermal expansion without compromising system integrity. Analysis of such case studies promotes knowledge sharing and the implementation of effective engineering solutions across the industry.
Challenges Faced by Piping Stress Analysts
Identifying Common Issues in Piping Systems
Piping stress analysts face various challenges while assessing piping systems. Common issues include:
- Corrosion: Over time, pipes can corrode, leading to compromised structural integrity and increased susceptibility to stress fractures.
- Thermal Expansion: Changes in temperature can cause pipes to expand or contract, leading to misalignment and increased stress.
- Dynamic Loads: External factors, such as vibrations from nearby machinery or seismic activity, can create unpredictable stressors in piping systems.
Mitigation Strategies for Stress-Related Problems
To address these challenges, several mitigation strategies can be employed:
- Regular Inspections: Routine monitoring of pipe conditions can identify corrosion or physical damage before it leads to failures.
- Flexible Design Considerations: Incorporating flexible joints and expansion loops can help accommodate thermal movement without generating excessive stress.
- Load Redistribution: Proper placement of supports and hangers can ensure that loads are evenly distributed, reducing stress concentrations.
Tools and Software for Effective Analysis
Utilizing advanced software tools enhances the precision of piping stress analyses. Programs such as AutoPIPE, CAESAR II, and ANSYS provide engineers with the capabilities to simulate conditions, analyze stresses, and optimize designs effectively. These tools come equipped with modules for specific analyses, such as dynamic response or thermal expansion, tailored to meet various project demands.
Best Practices in Piping Stress Analysis
Recommendations for System Design
The design phase is critical for successful piping stress analysis. Recommended best practices include ensuring that material choices align with operational conditions—such as temperature and pressure—and accommodating for thermal expansion in designs. Additionally, evaluating flow dynamics during the design allows for efficient routing that minimizes bends and junctions, further reducing potential stress points.
Quality Assurance and Compliance Standards
Establishing a strong quality assurance framework helps ensure that piping systems meet stringent industry standards. Organizations must adhere to guidelines set forth by regulatory bodies, such as the American Society of Mechanical Engineers (ASME) or the American Petroleum Institute (API). Regular audits, peer reviews, and documentation practices are vital to maintaining compliance and achieving design integrity.
Industry-Specific Guidelines for Optimal Results
Different industries have unique requirements for piping stress analysis. For example, the chemical processing industry may necessitate additional safeguards for handling corrosive materials, while the pharmaceutical sector must comply with stringent cleanroom standards. Tailoring analyses to meet industry-specific guidelines ensures that piping systems not only function efficiently but also adhere to the requisite safety and performance standards.
Future Trends in Piping Stress Analysis
Innovations Shaping the Industry
The field of piping stress analysis is witnessing rapid technological advancements. Innovations such as machine learning and artificial intelligence are providing new avenues for predictive analysis, helping engineers foresee potential issues before they arise. With the aid of artificial intelligence, systems can analyze historical data and recognize patterns that indicate potential stress failures, allowing for proactive maintenance and design alterations.
Integration with Digital Twin Technology
Digital Twin Technology is a game-changer in piping stress analysis. By creating virtual replicas of physical piping systems, engineers can simulate various operational conditions over time, enabling predictive maintenance and real-time monitoring for stress-related anomalies. This integration facilitates enhanced decision-making and more efficient operations while reducing downtime and unplanned outages.
Predictions for Market Growth and Evolution
As industries expand and evolve, the demand for sophisticated piping stress analysis continues to grow. Industry experts predict a substantial increase in the market for piping engineering services, driven by heightened safety standards and the need for robust piping systems in complex industrial processes. Furthermore, the drive toward sustainable practices ensures piping analysis will continue to adapt, incorporating environmentally friendly materials and designs that minimize ecological footprints.