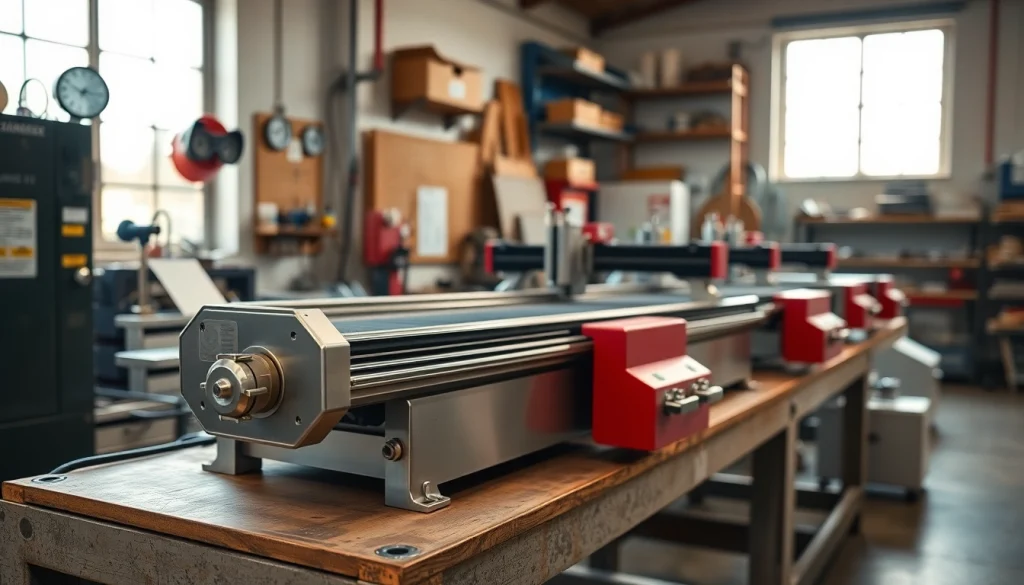
Understanding Cutting Equipment Basics
In myriad industries, from manufacturing to construction, the effectiveness and precision of cutting operations rely heavily on the tools employed. Cutting equipment comes in various forms, serving multiple purposes, from slicing metal and wood to performing intricate surgical operations. Understanding the fundamentals of cutting equipment is essential for anyone involved in these sectors, whether you’re purchasing new tools, seeking to improve workflow efficiency, or just trying to expand your knowledge.
What is Cutting Equipment?
Cutting equipment refers to tools specifically designed to cut through different materials. Tools in this category can range from handheld devices like knives and saws to sophisticated machinery, such as CNC (Computer Numerical Control) machines. Typically, these tools employ various cutting techniques, including slicing, shearing, and grinding, adapted to the materials and the desired end products. Effective cutting requires a keen understanding of the equipment’s properties, the materials involved, and the techniques employed.
Types of Cutting Tools
The range of cutting tools is vast, with each type tailored for specific applications:
- Hand Tools: These include utility knives, chisels, and hand saws, offering convenience and precision for small projects and delicate materials.
- Power Tools: Such as circular saws, jigsaws, and angle grinders, these tools provide enhanced performance and speed for larger projects.
- CNC Machines: These computer-controlled tools are used in industrial settings for precision cutting of materials like metal, wood, and plastics.
- Laser Cutters: Utilizing focused laser beams, these devices offer high precision and are often employed in advanced manufacturing processes.
- Water Jet Cutters: This method involves using high-pressure water jets mixed with abrasives for precise cutting without generating heat.
Applications of Cutting Equipment
Cutting equipment finds its application across numerous sectors:
- Manufacturing: Used extensively for cutting metals, plastics, and other materials needed in assembly lines.
- Construction: Tools like saws and chisels are fundamental for cutting wood and other construction materials.
- Aerospace and Automotive: Precision cutting is crucial for manufacturing components subject to strict safety and performance standards.
- Healthcare: Surgical tools designed for precise cutting during operations exemplify the importance of cutting equipment in medicine.
Key Features of Quality Cutting Equipment
When investing in cutting equipment, several critical features should be considered to ensure durability, efficiency, and safety:
Material Composition and Durability
The material used in manufacturing cutting tools significantly impacts their performance. High-speed steel (HSS), carbide, and cobalt are commonly used for their effectiveness in retaining sharp edges and enduring high temperatures during cutting. Durability is also paramount, as tools need to withstand rigorous use over time, especially in industrial settings. The best cutting tools boast superior wear resistance and hardness without compromising the delicate balance of flexibility needed to avoid breaking.
Precision and Accuracy
Quality cutting equipment is engineered for precision. Whether using a manual tool or a CNC machine, the ability to make accurate cuts ensures product consistency and reduces material waste. Features such as depth control, laser guidance, or automatic feeds can greatly enhance cutting precision. Additionally, measuring tools incorporated into cutting machines can provide real-time data on tolerances and dimensions, further optimizing accuracy.
Safety Considerations in Cutting Tools
Safety should always be a top priority when using cutting equipment. Tools equipped with safety features like blade guards, automatic shutoff switches, and ergonomic designs reduce the risk of injury. Training is also crucial for operators, including understanding tool functionality, appropriate personal protective equipment (PPE), and hazard recognition. Regular inspections and maintenance can help prevent accidents and prolong the life of the tools.
Choosing the Right Cutting Equipment for Your Needs
Selecting the proper cutting equipment requires careful consideration of project demands, available options, and financial resources. Here’s how to guide this important decision:
Assessing Project Requirements
Every project comes with unique requirements that dictate the type of cutting equipment needed. Start by evaluating the materials involved, the complexity of the cuts, and the desired production pace. For instance, intricate designs and high-volume cutting may necessitate advanced technologies like CNC machines, while simple home repair projects can efficiently utilize hand tools. Understanding the work’s scope will lead to more informed equipment choices.
Comparing Brand Options
The market for cutting equipment is bustling with various manufacturers, each claiming superiority in quality and innovation. When comparing brands, consider factors such as reliability, warranty provisions, customer support, and reviews from other professionals. Conducting thorough research on specific brands can reveal insights into their reputation and performance, assisting in making an informed choice.
Budgeting for Cutting Equipment
Your budget will significantly influence your cutting equipment selections. While cheaper tools may seem attractive, they often lack the longevity and performance levels of higher-quality options. It is crucial to assess your budget in conjunction with projected ROI based on the intended equipment use. Investing a bit more in top-tier equipment can yield long-term savings through reduced repair costs and improved efficiency.
Maintenance and Care for Cutting Equipment
Proper maintenance is essential to extend the lifespan of cutting tools and keep them operating at peak performance. Here are some best practices to consider:
Regular Cleaning and Maintenance Tips
After each use, proper cleaning helps to prevent the buildup of residues that can affect performance. For hand tools, this may involve wiping down blades with a cloth and applying a protective lubricant. Machinery may require more thorough cleaning, including coolant changes and examination for debris accumulations. Scheduling regular maintenance checks, based on usage frequency, can mitigate performance issues.
Identifying Wear and Tear
Recognizing signs of wear and tear early can avoid catastrophic tool failures. Common indicators include dull blades, irregular cutting patterns, or unusual noises during operation. Operators should routinely inspect tools for visible damage, checking sharpened edges and ensuring parts are functioning as intended. Replacing worn parts proactively can maintain cutting accuracy and extend tool longevity.
Storing Cutting Equipment Safely
Storage practices significantly impact the longevity and safety of cutting tools. Tools should be stored in a clean, dry environment to prevent corrosion and physical damage. Employing organizers such as toolboxes or pegboards can help keep cutting tools accessible while ensuring their safety. For power tools, unplugging and disconnecting from power sources before storage reduces the risk of accidents.
Future Trends in Cutting Equipment Technology
The landscape of cutting equipment is continuously evolving with innovations that enhance performance, usability, and sustainability. Understanding these trends can help businesses remain competitive and efficient.
Advancements in Precision Cutting
Modern cutting equipment is increasingly focused on precision. Technologies such as laser and waterjet cutting offer unparalleled accuracy, allowing intricate designs with minimal material waste. Moreover, improvements in CAD (Computer-Aided Design) software have streamlined the process from concept to execution, facilitating quicker project turnaround times. As machining technologies advance, manufacturers must stay abreast of these innovations to keep pace with industry standards.
Smart Cutting Equipment Integration
The integration of IoT (Internet of Things) devices is revolutionizing cutting equipment. Smart machines equipped with sensors can provide real-time data analytics, enabling users to monitor equipment performance, predict maintenance needs, and optimize cutting processes. Remote monitoring capabilities help businesses improve workflow management by providing data-driven insights into operational efficiency.
Sustainability in Tool Manufacturing
As industries shift toward sustainable practices, cutting equipment manufacturers are also adopting eco-friendly materials and processes. Innovations include recyclable materials for tool manufacturing and energy-efficient machines that consume less power during operation. Supporting sustainable brands not only contributes to environmental wellness but can also enhance a company’s image and appeal to conscientious consumers.