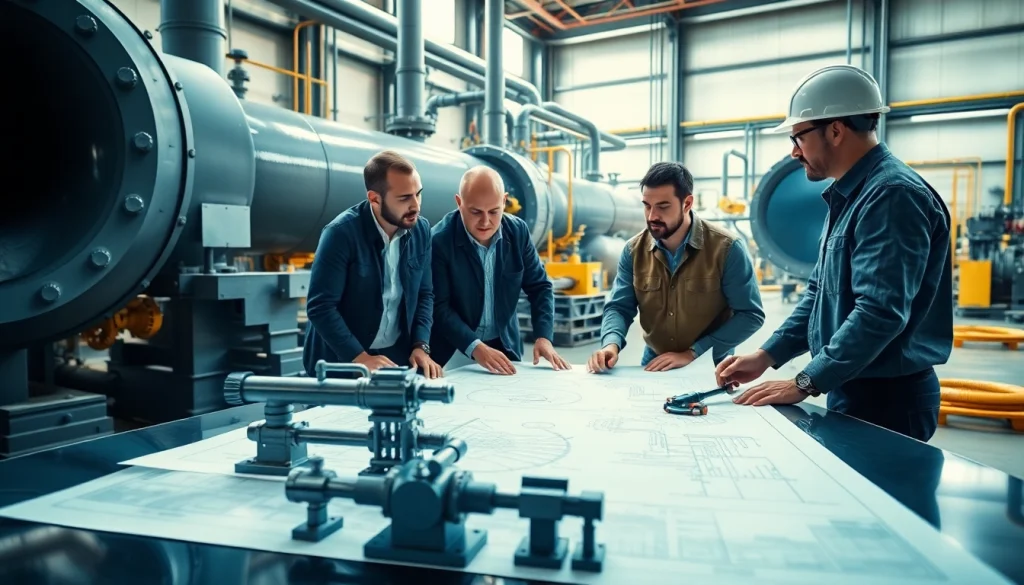
Understanding Piping Stress: Basics and Importance
Defining Piping Stress and Its Impact
Piping stress refers to the internal forces that arise within piping systems due to various operational conditions. These stresses can significantly affect the mechanical integrity of the system, potentially leading to failure if not adequately managed. Understanding piping stress is crucial for engineers and operators, as the repercussions can range from minor leaks to catastrophic failures that disrupt operations and pose substantial safety risks.
A piping stress Company, which specializes in analyzing and addressing these stresses, plays an essential role in maintaining the reliability and safety of piping systems across various industries, including oil and gas, chemical processing, and power generation.
Common Causes of Piping Stress in Engineering
Various factors contribute to piping stress, including:
- Thermal Expansion: Changes in temperature can cause materials to expand or contract, introducing stress if the piping system is rigid.
- Fluid Pressure: The pressure of the fluid within the pipes induces stress on the material, particularly at bends and supports.
- Weight of the Piping System: Dead weight from the pipes themselves, along with the weight of connected equipment and insulation, can lead to sagging and bending stresses.
- Seismic and Wind Forces: External forces from seismic activities or wind can introduce additional stress, particularly in elevated piping systems.
The Role of a Piping Stress Company in Industry
A piping stress company conducts rigorous analyses to ensure that systems can accommodate these stresses safely. Their expertise encompasses:
- Design Support: Assisting in the design phase to select materials and configurations that minimize stress.
- Stress Analysis: Utilizing software and analytical methods to model stresses under various operational scenarios.
- Inspection and Maintenance: Providing ongoing monitoring and evaluation services to detect issues before they lead to failures.
Key Factors Influencing Piping Stress
Temperature Effects and Material Considerations
Temperature is a significant contributor to piping stress. Materials have specific coefficients of thermal expansion, which dictate how much they will expand or contract with temperature fluctuations.
Choosing materials for piping systems involves considering their temperature ratings and how they behave under different thermal conditions. For instance, stainless steel may be preferred over carbon steel in high-temperature environments, as it retains its strength better when exposed to heat.
Fluid Dynamics: Understanding the Flow
The nature of the fluid being transported—its density, viscosity, and flow rate—affects the stresses experienced by the piping. For example, higher flow rates can lead to increased pressure drops and turbulence, which must be factored in during design and analysis. Understanding fluid dynamic principles helps engineers plan for potential stress points.
Additionally, routing and the design of bends and fittings influence fluid flow and, consequently, stress distribution along the pipelines.
Seismic and Wind Loads on Piping Systems
Piping systems are often exposed to environmental forces that can induce significant stress. In regions prone to earthquakes, seismic analysis becomes vital to ensure systems can withstand ground movements. Engineers must design supports and anchors strategically to mitigate these forces.
Wind forces, particularly on elevated piping structures, can also lead to increased stress and fatigue over time. Engineers assess historical weather patterns and expected gust speeds to incorporate appropriate design features.
Effective Piping Stress Analysis Techniques
Advanced Software Solutions for Stress Analysis
Modern engineering heavily relies on advanced software solutions for piping stress analysis. Programs like CAESAR II and AutoPIPE facilitate detailed modeling and simulation, allowing engineers to visualize stress distributions and identify potential failure points.
These tools also enable scenario modeling, which helps teams assess the impact of various operational changes, such as increased fluid temperatures or pressures. This predictive capability is essential for proactive maintenance and design adjustments.
Manual Calculation Methods for Quick Assessments
While software offers comprehensive analysis options, manual calculations still have their place, especially for quick assessments or when resources are limited. Engineers can utilize established formulas that calculate stress based on load, geometry, and material properties.
These methods can serve as a first check before more in-depth analysis is conducted, ensuring that major issues are addressed early in the design phase.
Case Studies: Successful Implementation of Stress Analysis
Numerous case studies illustrate the importance of thorough stress analysis:
- Project A: A chemical processing facility faced ongoing leaks at a junction point. An analysis using advanced software identified that thermal expansion was causing excessive stress. By redesigning the support structure and incorporating flexible joints, the facility significantly extended the life of the piping.
- Project B: An oil and gas transmission project underwent a seismic analysis, leading to the installation of additional bracing and expansion joints that minimized the risk of failure during potential earthquakes.
Best Practices for Piping Design and Maintenance
Regular Inspection and Monitoring Techniques
To maintain a safe and efficient piping system, regular inspection and monitoring are crucial. Techniques such as ultrasonic testing and infrared thermography allow for real-time monitoring of conditions and early detection of issues that could lead to piping stress.
A schedule for periodic assessments should be established, taking into consideration the operating environment and the criticality of the piping systems involved.
Design for Flexibility in Piping Systems
Incorporating flexibility into piping design can greatly reduce the risk of stress-related issues. Key strategies include:
- Using Expansion Joints: Integrating expansion joints enables the system to absorb some of the stresses related to thermal movements.
- Strategic Supports: Designing supports that allow for slight movements can help mitigate rigid stress concentrations.
Implementation of Safety Standards and Regulations
Adhering to safety standards and industry regulations is non-negotiable. Regulatory bodies such as ASME (American Society of Mechanical Engineers) provide guidelines that help engineers design piping systems that can safely withstand expected loads and environmental influences. Compliance with these standards not only enhances safety but also protects businesses from legal liabilities.
Evaluating Performance and Metrics for Success
Key Performance Indicators for Piping Systems
Setting clear Key Performance Indicators (KPIs) is essential for evaluating the performance of piping systems. Common KPIs include:
- Failure Rate: Monitoring the frequency of system failures and the causes behind them.
- Maintenance Costs: Tracking costs associated with repairs and preventative maintenance.
- Operational Downtime: Measuring the amount of time the system is non-operational due to stress-related issues.
Benchmarking Stress Analysis Results
Benchmarking allows organizations to compare their piping stress performance against industry standards or competitors. This helps identify areas for improvement and best practices that can be adopted to enhance system reliability.
Engaging with industry groups or utilizing data from research organizations can provide valuable insights into what constitutes leading practices.
Continuous Improvement through Feedback and Data
Continuous improvement is integral to effective piping system management. Utilizing feedback from maintenance teams, system operators, and data from monitoring technologies helps organizations refine their approaches to piping stress. Implementing a systematic feedback loop ensures that lessons learned from past experiences are incorporated into future designs and operational protocols.