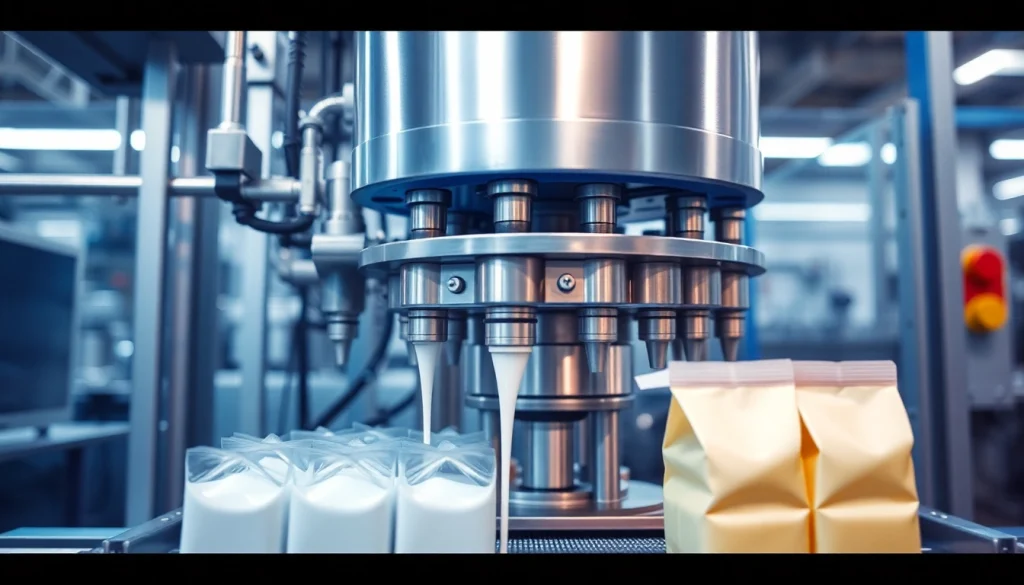
Understanding Liquid Packaging Machines
What is a Liquid Packaging Machine?
A liquid packaging machine is designed to fill, seal, and package liquids—ranging from beverages to chemical solutions—efficiently and effectively. These machines are crucial in various industries, including food and beverage, pharmaceuticals, cosmetics, and chemicals. They are engineered to ensure that products are packaged in a way that maintains their quality, extends shelf life, and complies with industry standards.
Liquid packaging machines utilize various technologies such as volumetric filling systems, gravimetric systems, and vacuum sealing techniques. This variety allows manufacturers to choose a machine that best fits their product type and packaging requirements. When selecting a Liquid Packaging Machine Supplier, it’s important to consider the specific features of the machines they offer, including accuracy, speed, and compatibility with various container types.
Key Functions and Features
Liquid packaging machines come equipped with several key functions that enhance their usability and efficiency:
- Filling Precision: Machines are designed to deliver accurate volumes of liquids, reducing waste and ensuring product quality.
- Material Compatibility: Many machines can handle a variety of liquid viscosities, from water to thicker substances like sauces or creams.
- Sealing Mechanisms: A good packaging machine will have strong sealing capabilities to prevent leaks and contamination.
- User-Friendly Interfaces: Modern machines often feature intuitive controls and monitoring systems to simplify operation.
- Customization: Many suppliers offer machines that can be tailored to meet specific packaging needs, such as unique bottle shapes or sizes.
Applications Across Industries
The versatility of liquid packaging machines allows them to be utilized in various sectors:
- Food and Beverage: From soft drinks to sauces, these machines help ensure products are packaged under hygienic conditions.
- Pharmaceuticals: Precision is vital in this industry for liquid medications, necessitating highly accurate filling systems.
- Chemicals: Many chemicals require specialized packaging to prevent corrosion or contamination, making robust packaging solutions essential.
Choosing the Right Liquid Packaging Machine Supplier
Evaluating Supplier Reputation and Experience
When choosing a liquid packaging machine supplier, reputation and experience in the industry are critical. Established suppliers often have a proven track record of providing reliable equipment that meets regulatory standards.
Researching a supplier’s history, reading customer reviews, and checking their portfolio can give you valuable insights into their reliability. Ask for case studies or references from similar industries to understand how well their machines perform in actual production environments.
Understanding Machine Specifications and Capabilities
Before making a purchase, you must understand the machine specifications and capabilities:
- Filling Speed: Consider how quickly the machine can fill containers, which impacts overall production efficiency.
- Container Compatibility: Ensure the machine can handle the specific shapes and sizes of containers you will be using.
- Automation Level: Decide between manual, semi-automatic, and fully automatic systems based on your production scale.
Customer Support and After-Sales Service
Good customer support is crucial for maintaining productivity. Ensure the supplier offers comprehensive after-sales services, including installation, training, and ongoing maintenance. A supplier that provides quick response times to service requests can help minimize downtime in production.
Types of Liquid Packaging Machines
Automated vs. Manual Systems
Understanding the differences between automated and manual liquid packaging machines is crucial:
- Automated Systems: These machines are highly efficient and require minimal human intervention, making them ideal for high-volume production. They often feature advanced technologies for precise filling and capping.
- Manual Systems: Usually more affordable, manual systems are better suited for small-scale operations. However, they require more labor and may pose greater risk for human error.
Common Machine Configurations
There are several configurations of liquid packaging machines available, including:
- Piston Fillers: Best for thick or viscous liquids, as they provide a consistent volume per cycle.
- Pressure Fillers: Ideal for carbonated beverages, utilizing pressure to push liquid into containers while reducing foam.
- Gravity Fillers: Suitable for thinner liquids, where the force of gravity fills the container.
Innovative Technologies in Liquid Packaging
Technology in the liquid packaging industry is advancing rapidly. Innovations such as automated assembly lines, real-time monitoring systems, and smart sensors are becoming increasingly common. These technologies not only improve efficiency but also enhance safety standards by minimizing human contact with hazardous materials.
Best Practices for Operating Liquid Packaging Machines
Maintenance Tips for Longevity
Regular maintenance is essential for the longevity of any liquid packaging machine. Consider these best practices:
- Scheduled Inspections: Regular checks can identify wear and tear before they result in costly repairs.
- Cleanliness: Keeping the machinery clean helps prevent contamination and ensures the quality of packaged products.
- Technical Upgrades: Stay updated with the latest technology to improve efficiency and productivity.
Ensuring Compliance with Industry Standards
Compliance with industry standards is a must. Familiarize yourself with regulations from organizations like the FDA or relevant local authorities regarding packaging materials and practices. Regular audits and training can help ensure adherence to these standards.
Training Personnel for Optimal Performance
Investing in personnel training is crucial. Employees should understand the operation of the machinery and the importance of adhering to quality control measures. Regular workshops and refreshers can enhance their skills and reduce the risk of operating errors.
Future Trends in Liquid Packaging
Sustainability and Eco-Friendly Practices
As environmental concerns grow, there is a significant shift towards sustainability in packaging. Liquid packaging machine suppliers are increasingly focusing on eco-friendly materials, like biodegradable plastics and recyclable packaging, to meet consumer expectations.
Integrating Smart Technology
Smart technology is revolutionizing the packaging industry. IoT-enabled machines can now provide real-time data analytics to manufacturers, enabling predictive maintenance and efficiency insights. This kind of smart integration can streamline operations and significantly reduce downtime.
The Impact of E-Commerce on Packaging Solutions
The rise of e-commerce is reshaping packaging solutions. Liquid packaging machines are being designed to accommodate smaller, retail-ready packaging that is not only convenient for online shoppers but also minimizes shipping costs. The focus is on creating protective yet light packaging that can withstand the rigors of transportation.