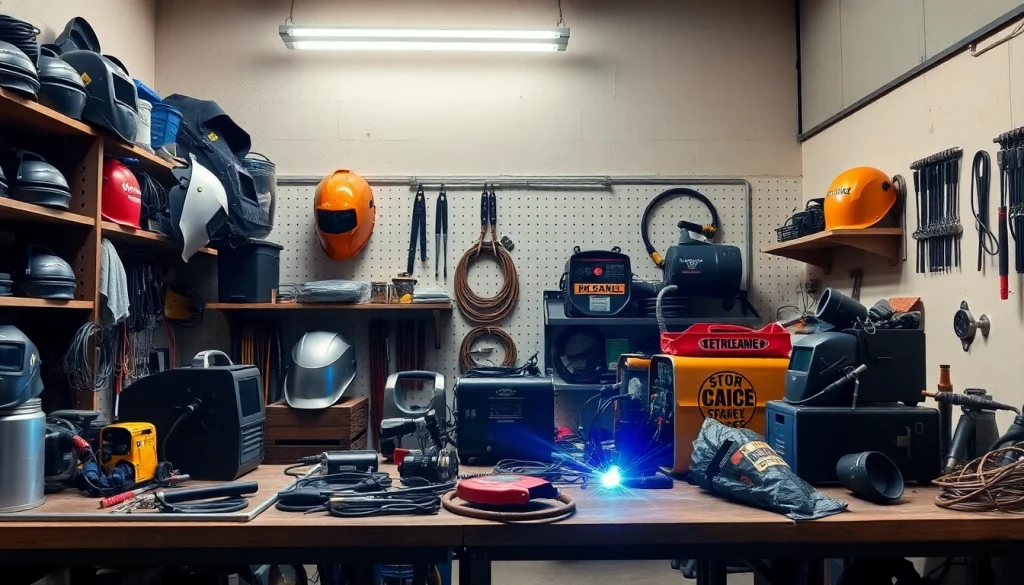
Understanding Welding Supplies
Welding is an essential process in multiple industries, from manufacturing to construction. It involves joining metals and thermoplastics through the application of heat and, in some cases, pressure. Quality welding supplies are crucial for ensuring that these processes are carried out effectively and safely. This article aims to provide an extensive overview of welding supplies, encompassing everything from essential equipment to maintenance practices.
Overview of Essential Supplies
Welding supplies encompass a wide range of tools and materials essential for different types of welding projects. The primary equipment includes:
- Welders: These machines generate the necessary heat to melt the workpieces for joining. Common types include MIG (Metal Inert Gas), TIG (Tungsten Inert Gas), and Stick welders.
- Protective Gear: Safety is paramount in welding. Essential gear includes welding helmets, gloves, jackets, and respiratory protection to safeguard against sparks and fumes.
- Consumables: These include welding rods, wires, and gas. Each type is specific to the welding technique used and directly affects weld quality.
- Accessories: Tools such as clamps, magnets, and cleaning equipment are necessary for workspace organization and ensuring precision during welding.
Different Types of Welding Processes
Understanding the various welding processes is crucial for selecting the proper supplies:
- MIG Welding: A popular choice due to its ease and speed, MIG welding uses a continuous wire feed as an electrode and an inert gas to shield the weld from contamination. Supplies needed include a MIG welder, shielding gas (typically argon), and welding wire.
- TIG Welding: This method provides high-quality welds but requires more skill. It uses a non-consumable tungsten electrode and a separate filler material. Important supplies include a TIG welder, tungsten electrodes, and appropriate shielding gas.
- Stick Welding: Known for its versatility, it’s often used in outdoor conditions. It employs a consumable electrode and is effective in accessing hard-to-reach areas. Supplies include stick welding rods and a reliable stick welder.
- Flux-Cored Arc Welding (FCAW): Similar to MIG, but the wire acts as its own shielding gas, making it suitable for outdoor applications. Essential supplies include flux-cored wire and compatible equipment.
Choosing the Right Equipment for Your Needs
When selecting welding supplies, consider the following aspects:
- Project Requirements: Assess the type of metal and thickness you will work with, as this dictates the welding process.
- Experience Level: Beginners may find MIG welding more manageable, while experienced welders might prefer TIG or Stick welding for more advanced tasks.
- Portability: If you will be working on-site, consider the weight and size of the welder along with its power source.
- Budget: Set realistic expectations for quality versus cost. Investing in reputable brands can offer better durability and performance.
Top Brands of Welding Supplies
The market is flooded with numerous brands, each with its strengths and weaknesses. Understanding leading brands is beneficial for making informed purchasing decisions.
Comparison of Leading Brands
Some of the top brands in welding supplies include:
- Miller Electric: Known for high-quality welding machines and safety equipment, Miller products are widely used across various industries.
- Lincoln Electric: Offers a range of welding and cutting equipment renowned for innovative technologies that cater to both beginners and professionals.
- ESAB: Focuses on the entire welding process, providing machines, consumables, and accessories, prioritizing efficiency and quality.
Cost vs. Quality: What to Consider
In welding equipment, cost often correlates with quality. While budget options may seem appealing, they often lack durability and functionality, leading to higher long-term costs due to repairs and replacements. Therefore, invest in well-reviewed equipment that complements your needs, emphasizing reliability and performance.
Customer Reviews and Recommendations
Reading customer reviews can provide insights into the performance and reliability of specific welding supplies. Online platforms and welding forums can be good sources of information where users share their experiences. Look for equipment that consistently receives positive feedback regarding ease of use, safety features, and overall effectiveness.
Where to Buy Quality Welding Supplies
The source of your welding supplies can significantly impact the quality and price you will pay. Here are a few avenues to consider:
Online vs. In-store: Pros and Cons
Purchasing welding supplies online offers several advantages:
- Convenience: Shop 24/7 without the need to travel.
- Variety: Easy access to a wide range of brands and products.
- Price Comparisons: Easily compare prices between multiple suppliers.
However, in-store shopping allows for immediate access to products, as well as the opportunity to consult with knowledgeable staff who can provide expert recommendations.
Finding Local Suppliers
Local suppliers can often provide immediate solutions and personalized service. Search for suppliers using online maps or business directories. Additionally, visiting local trade shows can help you discover nearby suppliers while allowing you to see products firsthand.
Understanding Shipping and Returns Policies
When purchasing online, always review the shipping and returns policy. Ensure that the supplier offers reasonable shipping fees and understands the return process to avoid issues with defective products. Clear policies protect your investment and provide peace of mind with your purchases.
Maintenance and Safety for Welding Supplies
Proper maintenance and safety practices are critical for producing quality welds and ensuring user safety. Here are essential tips for both:
How to Maintain Your Welding Equipment
Regular maintenance prolongs the life of your welding equipment. Follow these practices:
- Clean Your Equipment: Regularly clean the welding tips and nozzles to prevent clogging and ensure optimal performance.
- Inspect for Damage: Regularly check cables, hoses, and connectors for wear and tear. Replace any damaged parts immediately.
- Store Properly: Keep equipment in a dry, clean location to prevent corrosion and damage from environmental factors.
Safety Gear Essentials for Welders
Welders must prioritize safety to prevent workplace accidents. Essential safety gear includes:
- Welding Helmet: Protects the eyes and face from arc flashes, sparks, and heat.
- Gloves: Heavy-duty gloves protect against heat and sharp metal edges.
- Protective Clothing: Wear flame-resistant clothing that covers the arms and legs to prevent burns.
- Respiratory Protection: In environments where fumes are present, a proper respirator is essential to protect lung health.
Common Safety Practices
To ensure safety while welding, follow these practices:
- Work in a Well-Ventilated Area: Adequate ventilation prevents the accumulation of harmful fumes.
- Use Proper Lifting Techniques: Be cautious when moving heavy equipment or materials to prevent injury.
- Have a Fire Extinguisher on Hand: Be prepared for any potential fire hazards created by welding processes.
Advanced Welding Techniques and Supplies
As welders advance in their skills, they may find themselves integrating more sophisticated techniques and tools into their workflows. Here, we explore new tools and trends in welding.
Integrating New Tools into Your Workflow
Advanced welding techniques often require specialized tools. Common upgrades may include:
- Automated Welding Systems: Useful for increasing efficiency, especially in large production environments.
- Multi-process Welders: Allow for flexibility in types of welding performed, making them a wise investment for diverse projects.
- Heat Treatment Equipment: Essential for altering metal properties post-welding to improve strength and performance.
Consider taking a welding course to learn how to effectively integrate new tools into your projects.
Future Trends in Welding Supplies
The welding industry is evolving, with trends indicating a move towards more environmentally friendly processes, automation, and advanced materials. Expect to see increased use of:
- Green Technology: The development of eco-friendly welding techniques and materials that minimize environmental impact.
- Smart Welding Equipment: Integration of IoT (Internet of Things) technology in welding machines for better monitoring and troubleshooting.
- Advanced Materials: New materials that enhance performance and durability in welds.
Training Resources for Advanced Techniques
As welding technology advances, so should your skills. Several resources can help:
- Online Courses: Many platforms offer courses focusing on advanced welding techniques and safety practices.
- Trade Schools: Consider enrolling in a trade school that offers hands-on training with modern welding equipment.
- Webinars and Workshops: These often featured on industry websites can provide insights into the latest products and techniques.
Staying updated on industry innovations ensures you remain competitive in the field.