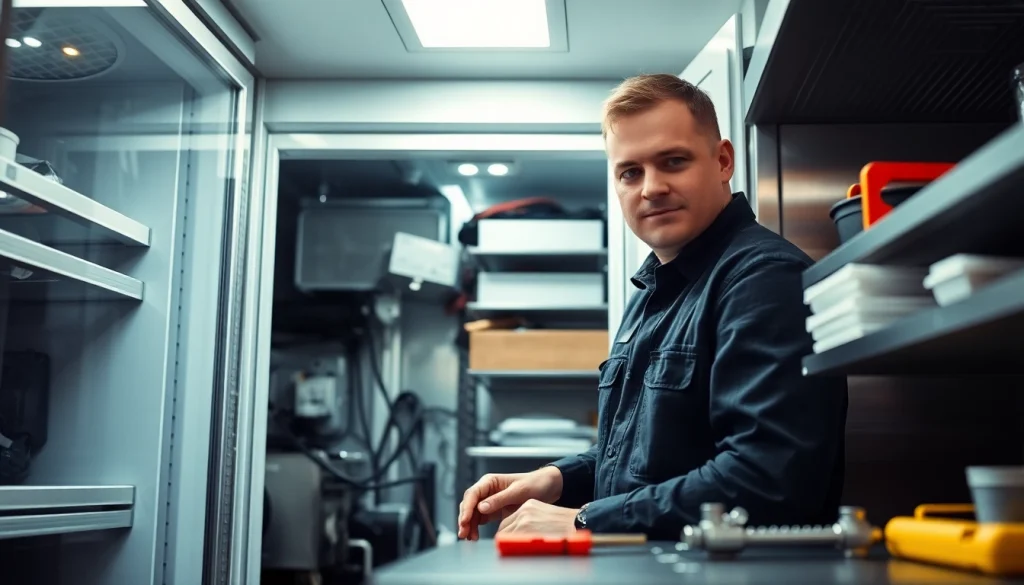
Understanding Walk in Freezer Repair
What is a Walk in Freezer?
A walk-in freezer is a large refrigeration unit that provides ample space for storing perishable items at subzero temperatures. Industries such as food service, grocery stores, and pharmaceutical companies frequently utilize these freezers to stock large quantities of products. Unlike standard freezers, which are typically found in residential kitchens, walk-in freezers offer a significant capacity that allows businesses to buy in bulk and keep their inventories effectively frozen. The construction of walk-in freezers includes insulated walls, ceilings, and floors to maintain consistency in temperature and minimize energy consumption.
Common Issues in Walk in Freezers
Despite their robust design and purpose, walk-in freezers can encounter several problems. Understanding these common issues can help business owners and maintenance personnel identify when professional walk in freezer repair is needed:
- Temperature Variability: One of the most critical issues, temperature fluctuations can jeopardize the integrity of stored products.
- Compressor Failure: This essential component circulates refrigerant and maintains the proper temperature. A failing compressor can result in inadequate cooling.
- Defrost Cycle Problems: If the defrost cycle fails, it can lead to excessive frost within the unit, which may cause blockages and reduced efficiency.
- Door Seal Issues: Worn or damaged door seals can cause cold air to escape, leading to increased energy costs and improper temperatures.
- Electrical Problems: Faulty wiring or control systems can result in system failures, requiring immediate inspection and repair.
Importance of Timely Repairs
Addressing repairs in a timely manner is paramount in the food and pharmaceutical industries. A malfunctioning walk-in freezer can lead to spoilage, waste, and expensive inventory loss. Quick diagnosis and repairs help avoid detrimental downtime and ensure that products remain at safe temperatures.
Additionally, regularly scheduled maintenance can extend the lifespan of a walk-in freezer, saving businesses money in the long run. Implementing an effective repair strategy not only safeguards against unanticipated costs but also enhances the overall efficiency of the refrigeration system.
Signs You Need Walk in Freezer Repair
Temperature Fluctuations
One of the most telling signs that your walk-in freezer requires repair is if you notice temperature inconsistencies. Frequent temperature swings can compromise food safety and the integrity of other stored items. If you find that temperatures are rising unexpectedly, inspecting the thermostat and monitoring system for faults should be among your first steps.
Unusual Noises
Sounds emanating from the freezer that deviate from its usual operational hum often indicate underlying issues. Odd noises, such as banging, clattering, or persistent clicking, can signify problems with the compressor, fan, or evaporator. Ignoring these sounds may result in more severe malfunctions, necessitating comprehensive repairs.
Frost Build-Up
While frost is a natural occurrence in freezers, excessive build-up can block air circulation, reducing efficiency and leading to higher energy expenses. In particular, frost accumulation on evaporator coils or around fans must be addressed. Regularly monitoring frost levels and addressing any increases can help maintain optimal performance.
DIY Maintenance Tips for Your Walk in Freezer
Regular Cleaning Protocols
Maintaining a clean environment in your walk-in freezer is essential for its longevity and efficiency. Regular cleaning helps prevent the build-up of frost and ensures that air can circulate freely. Here are some practical steps:
- Schedule monthly deep cleanings that include scrubbing surfaces and removing debris.
- Use non-abrasive cleaners suitable for stainless steel to avoid damaging the surfaces.
- Regularly clean the evaporator and condenser coils to ensure optimal cooling efficiency.
Monitoring Temperature
Investing in a temperature monitoring system can save businesses time and money in the long run. Regularly checking temperature logs helps identify fluctuations before they escalate into significant issues. Many digital monitoring devices will alert managers immediately upon detecting temperature deviations, allowing for swift action.
Checking Door Seals and Gaskets
Door seals and gaskets play a vital role in maintaining internal temperature. Inspect them regularly for signs of wear and replace them when necessary to prevent air leaks. Even minor gaps can result in significant energy loss, leading to higher operating costs.
Choosing a Professional for Walk in Freezer Repair
Qualities to Look For
Selecting the right professional for your walk-in freezer repair is imperative for ensuring reliable service. Here are some qualities that set a competent technician apart:
- Experience: Look for technicians with proven expertise in commercial refrigeration.
- Licensing and Certification: Ensure that the technician is certified and follows all local regulations.
- References and Reviews: Check for client testimonials and online reviews to gauge their service quality.
Questions to Ask Before Hiring
Before committing to a repair service, asking the right questions can help you make an informed decision:
- What is your response time for emergency repairs?
- Are you familiar with my specific walk-in freezer model?
- Can you provide a detailed estimate, including labor and parts?
- What warranties or guarantees do you offer on your work?
Benefits of Professional Services
While DIY repairs might seem tempting, the benefits of hiring a professional often outweigh the costs:
- Expertise: Professionals can quickly diagnose and fix issues that may not be immediately apparent to untrained eyes.
- Safety: Working with refrigeration systems involves inherent risks; professionals are better equipped to handle repairs safely.
- Warranty Protection: Many professional services offer warranties on their work, providing peace of mind in case issues arise post-repair.
Cost Factors in Walk in Freezer Repair
Average Repair Costs
Understanding the financial aspect of walk-in freezer repair helps businesses budget effectively. On average, the cost of repairs can vary widely based on the complexity of the issue and the required components. Simple repairs such as replacing gaskets may run as low as $100, while compressor replacements can set businesses back anywhere between $250 and $650. Regular maintenance and timely repairs can ultimately save businesses a significant amount in potential losses.
Preventive Maintenance Expenses
Investing in preventive maintenance can be more cost-effective than waiting for a complete breakdown. By budgeting for regular inspections and maintenance services, businesses can minimize unexpected repair costs and ensure their systems run efficiently. Typically, preventive maintenance contracts can range from $300 to $800 annually, depending on service frequency and complexity.
When to Consider Replacement
In certain cases, replacement may be more prudent than repair. Here are some indicators:
- If the repair costs exceed 50% of the unit’s total replacement cost.
- When the equipment exhibits recurring issues despite following a repair schedule.
- If the walk-in freezer is older than 15 years and increasingly inefficient.
Weighing these factors alongside operational needs and budget constraints will assist in making an informed decision.